FAQs
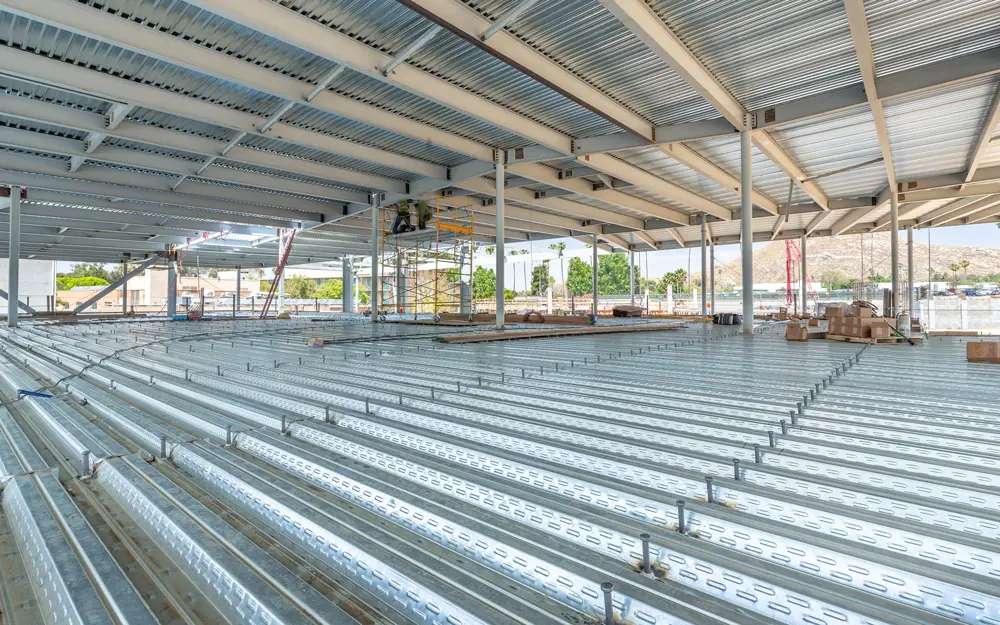
From installation techniques and design considerations to code compliance and maintenance practices, our FAQ page covers a wide range of common inquiries. Explore the FAQ page and empower yourself with the knowledge to make informed decisions and ensure successful steel deck projects.
How do I find a safe allowable span for a poured concrete slab on metal deck when deck is being used as a form?
The allowable span for common slab conditions may be found in SDI’s FDDM (Floor deck Design Manual) and can be purchased on this website. The designer should consider that the allowable span typically includes the Dead Load weight of the deck and concrete along with Construction Live load of 20 lb/ft2 or a 150-pound point load. Or a 50lb/ft2 un-poured load. If the construction live load will exceed these values before the concrete can harden, the designer should consult the deck manufacturer for advisement. The allowable spans may also be found on the Deck Manufacturer’s catalogs. If the required span exceeds the allowable span, shoring might be allowable depending on the slab condition.
How do I find the allowable load for my deck condition?
The allowable load tables for common slab conditions may be found in SDI’s FDDM (Floor deck Design Manual) and can be purchased on this website. The allowable load may also be found on the Deck Manufacturer’s catalogs. For composite floor deck, the load is often shown as a “Superimposed” load which is the allowable load of the hardened concrete slab on metal deck. For roof deck, the load is given for the bare metal deck. For form deck, both conditions may be shown. LRFD, ASD or LSD methodology may be used in these tables.
What is the difference between interlocking and nestable side laps?
Nestable side laps “nest” atop the adjacent panel with a lip that can be screwed, or seam welded. Interlocking side laps include a male lip that fits into the female lip and can be welded, or button punched. Upon request, Interlocking deck can often be requested with an “added return” on the female lip that allows the deck to have a screw attachment. Proprietary fasteners are also available.
Is Steel Deck fire resistant?
Steel has fire resistant properties, and therefore Steel Deck does. Steel is inherently fire-resistant because it has a high melting point and does not contribute fuel to a fire. It retains its structural integrity even when exposed to high temperatures. However, steel can lose its strength and deform under prolonged exposure to extreme heat. The fire resistance capability of a system depends on factors such the deck thickness, concrete depth (if poured) and what other fire resistance measures are used (such as spray-on fireproofing). The fire resistance of a steel deck system is typically tested and rated according to specific standards and regulations, such as those provided by organization like Underwriters Laboratories (UL) and can be found in their literature. This information can commonly also be found in the deck manufacturer’s brochure.
Do I need additional support for small holes in the deck?
Guidance for small openings in deck can be found in the “Deck Damage and Penetrations” White Paper or in the MOC (Manual of Construction).If the holes are small enough, only patching may be required. For larger openings and depending on the extent of the opening, channels or plates may be used to transfer the load to undamaged flutes. Additional framing may be required. Reinforcing channels or zees may be used to transfer loads from removed sections of roof for Sump Pan openings.
What is the difference between 1 1/2” form deck and 1 1/2” type ‘B’ roof deck?
Typically, there is no physical difference between 1 1/2” form deck and 1 1/2” type ‘B’ roof deck. 1 1/2” form deck is often installed in its inverted position when used as a concrete form for increased load carrying capacity.
Where can I find information on how to safely install metal deck?
Consult SDI’s Manual of Construction with Steel Deck. If welding is used as a method of attachment, it should be done in accordance with the Structural Welding Code, AWS D1.1 or D1.3. Installation must be performed by a qualified operator.
Why do load tables vary between metal deck manufacturers?
There are several reasons for differences between the tables.There can be differences in the yield strength of the material of which the calculations are made. The Differences may be due to the method of calculation for which the value is obtained. For example, flexural resistance of a composite slab can be determined using the “Prequalified Section”, the “Shear Bond” or the “Ultimate Strength” methods or performance testing. Some manufacturer’s tables include LRFD and others include ASD or LSD methodology, which would have different values. Differences can also be due to slight variation in profile shape between common profiles.
What type of light-gage flashings are used with steel deck?
End closures, pour stops, zee closures, column closures and girder or side closures are used with composite deck.Ridge caps, Flat plates and Sump pans are often used with roof deck. Consult the manufacturer’s brochure for more information. Design examples and A pour stop selection table are available in SDI’s FDDM (Floor deck Design Manual) and can be purchased on this website.
What types of finishes are available for steel deck?
Roof and Floor deck are available in several finishes depending on the manufacturer.Some typical finishes include Galvanized, Primer painted, or a combination of the two. Environmental conditions should be considered when selecting a finish and no deck is completely resistant to corrosion.
What is the maximum steel coil strength SDI member companies use?
The maximum coil strength widely available to member companies of SDI is 80 KSI while the maximum allowable design strength is 60 ksi. There are certain limitations. Member companies will pick and choose which proprietary profile they will roll with a higher strength coil. For more information, please see the list of member companies for availability.
What is the difference between a form deck and a composite deck?
Form deck works as a shape builder for the concrete or lightweight roofing material and is ultimately a stay in place form. Form deck is usually manufactured in maximum un-shored spans to provide a more economical approach to concrete or light weight insulation work. Composite decks are primarily used in floor systems. Composite deck is manufactured with a proprietary embossments to “grip” the concrete and are often paired with shear stud use, allowing the elevated composite slab to tie into the underneath supporting structure after the concrete slab has been poured and dried cured.
What is the maximum deck depth SDI member companies roll?
It varies, every commodity profile must meet the SDI minimum specified properties but every profile a member company rolls is proprietary to that company. Most SDI members roll profiles up to 3 inches deep, in line with profiles outlined by the SDI. Various manufacturers can supply proprietary profiles that are even deeper.
Where can I find the diaphragm strength in accordance with a specified fastener pattern?
Most SDI members will publish diaphragm strength in accordance with standard SDI attachment patterns. The strengths will slightly vary from manufacturer to manufacturer due to strength of available coil and section properties. Associate members of the SDI also produce proprietary fasteners and often provide associated capacities.
Is it better to specify a higher-grade deck over the yield outlined by the SDI?
It depends on the application. The flexural strength provided by yield decks is more significant but higher-grade steel lacks ductility. This can potentially pose as a problem for the erectors installing the deck.
Get in Touch
If you have any further questions or need additional assistance, please don’t hesitate to contact our team!